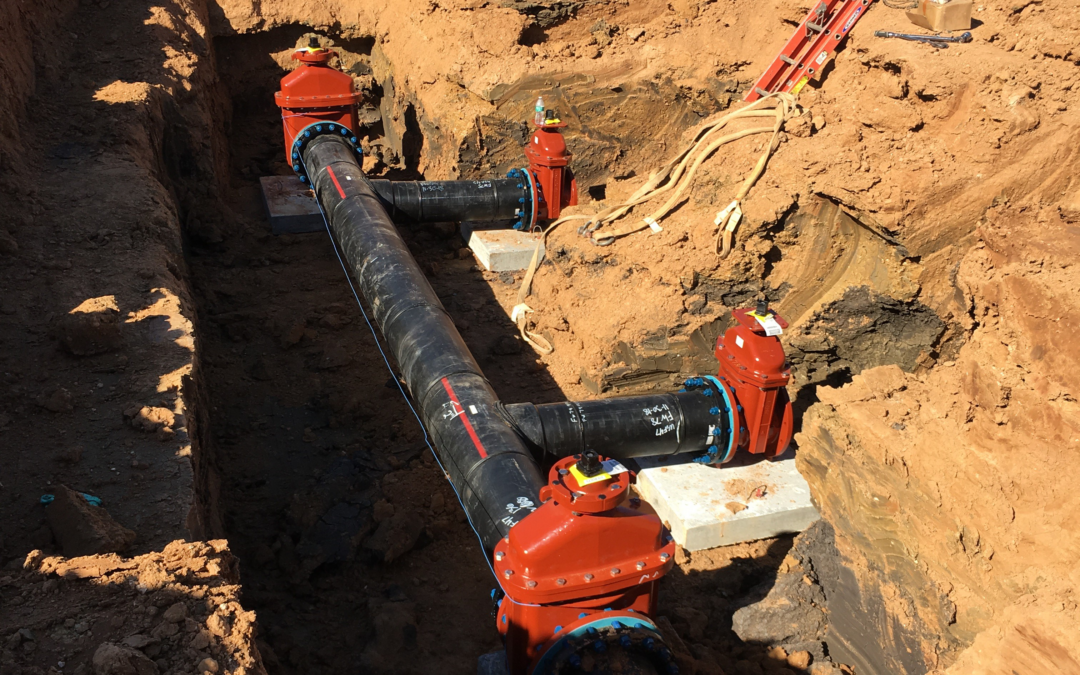
The Pipeline Hydrotesting Procedure Explained
Hydrotesting of pipelines is a critical process for ensuring the integrity and safety of pipelines. This plays a vital role in preventing leaks, failures, and costly disruptions. Hydrotesting verifies a pipeline’s ability to withstand the stress it will face during operation through a high-pressure test. This process helps identify weaknesses, such as cracks or structural issues, that could lead to eventual failure.
Conducting a Step-by-Step Hydrotesting Procedure
It is essential to meet the industry standards set by ASME hydrotest guidelines in order to ensure piplelines perform reliably under pressure. By following a detailed, step-by-step process, US FUSION can assess the structural integrity of pipelines, identify potential issues, and ensure compliance with industry standards.
Below is an outline of the key stages involved in conducting a successful hydrotest, from initial preparations to post-test analysis.
1. Preparation and Safety Checks
The first step in the hydrotesting procedure is ensuring all safety protocols are in place. The system should carefully be checked for cracks, leaks, or weak spots. All materials and components must meet the design specifications and ASME code requirements. Test pressure calculations should be checked to align with ASME hydrotest standards.
2. Filling the Pipeline
Once safety checks are complete, the pipeline is filled with water from the bottom up. This step ensures that all air pockets are removed, as air could cause inaccurate hydrotest pressure readings or interfere with the test.
3. Gradual Pressurization
The pipeline is gradually pressurized by pumping water into the system. The pressure is slowly increased to the designated hydrotest pressure. Monitoring the pressure increase is essential to avoid sudden pressure spikes that could damage the pipeline or equipment.
4. Stabilizing the Pressure
After reaching the desired hydrotest pressure, the pressure is allowed to stabilize for a set period determined by project requirements. During this time, the pressure gauge is carefully monitored to ensure it remains constant.
5. Leak Detection
The next step is to thoroughly inspect the pipeline for any signs of leaks. If the pressure drops at any time, it may indicate a leak or weakness in the pipeline. If leaks are identified, the pipeline will need to be repaired.
6. Deformation Monitoring
While the pipeline is under pressure, it’s important to monitor for any signs of deformation, such as bulging or movement. These issues can indicate structural weaknesses. If significant deformation is observed, the test may need further investigation.
7. Test Completion and Pressure Reduction
After the test duration is completed and no issues are found, the pressure is slowly reduced to normal levels. The pipeline is then safely depressurized, and the water is drained from the system.
8. Documentation of Results
Once the test is complete, a detailed report is generated. This report includes the test data, such as the hydrotest pressure levels, test duration, any leaks or issues detected, and corrective actions taken. Proper documentation is crucial for regulatory compliance and ensuring that the test was conducted correctly.
9. Post-Test Analysis
The final step involves analyzing the results of the hydrotest to determine whether the pipeline has passed or failed. If any issues were found, repairs or replacements will be necessary before the pipeline can undergo another test.
Tackling Common Hydrotesting Challenges
Two of the most common hurdles in hydrotesting are managing wastewater and addressing test failures, both of which require specialized solutions. A specialty construction company, such as US FUSION, is equipped to handle these challenges efficiently, ensuring smooth, safe, and compliant testing.
Handling Wastewater
One of the biggest environmental concerns during hydrotesting is the large volume of wastewater generated. After testing, the water used to pressurize the pipeline must be properly disposed of to avoid contamination. US FUSION employs filtration systems to treat and recycle the water, ensuring that it meets environmental standards before disposal.
Dealing with Test Failures
Another challenge is dealing with potential test failures. If a hydrotest identifies leaks, structural weaknesses, or other issues in the pipeline, quick action is needed to prevent delays. US FUSION’s team of experts is trained to identify the causes of failures quickly. Once the problem is identified, they can make repairs and modifications.
Let US FUSION Handle The Pipeline Hydrotesting Procedure
By combining innovative technologies, expertise, and a commitment to environmental and safety standards, US FUSION is able to effectively overcome the common challenges of hydrotesting. With over 35 years of diversified experience in specialty construction, our skilled experts have your back.